Previously, we’ve shown you actual cases of the SMT production line. Knowing the common SMT problems, we can effectively conduct inspections and tests for these issues. However, a high pass rate does not mean the quality, cost, and delivery (QCD) are controlled. In this article, you will recognize the importance of the pass rate and how Allion adopts an efficient system in SMT quality management.
First Pass Yield
First Pass Yield (FPY) is an indicator that measures the production quality of the production line used to describe a certain situation of production quality, work quality, or test quality. It refers to the yield rate of all procedures passed in one attempt, from the first step to the last step of the entire project. It’s also known as the first-time pass rate.
Formula: FPY = (Number of products passed in one attempt ÷ Total number of products) × 100%
Pass Rate
Since every step of the production line might produce defects, some can be fixed through remanufacturing, so the final pass rate cannot accurately reflect the losses caused in the process.
Formula: Pass Rate = (Final number of passed products ÷ Total number of products) × 100%
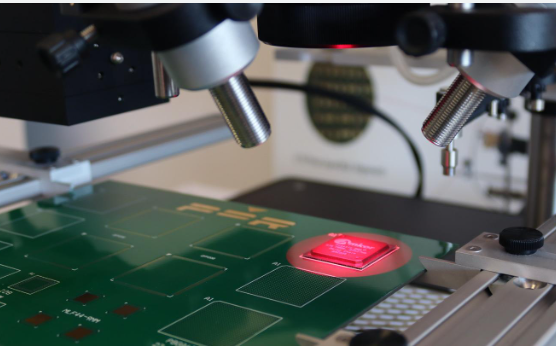
Example 1: BGA rework
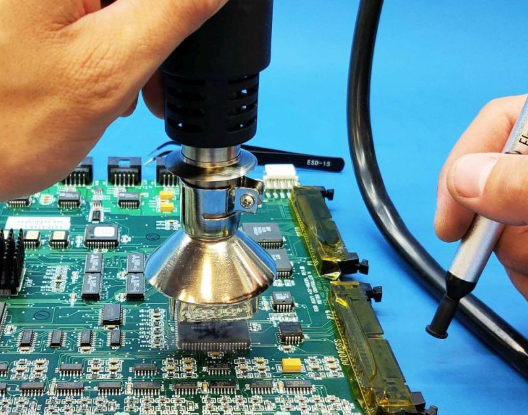
Example 2: SMD rework
From raw materials to the finished product, there are many procedures in between. During the manufacturing process, many semi-finished and finished products cannot follow the normal process due to poor processing. Some even needed to be stopped for repairs or scrapped. To prevent the pass rate from being too low, managers may modify data in the report, sometimes even covering up the truth.
For products that require multiple processes, the quality is evaluated by the traditional method of evaluating the pass rate. The pass rate is usually calculated by the number of good products in the last inspection procedure. Even if there are defective products, as long as they’re repaired and passes the last check, it’s regarded as good product. Therefore, there are limitations in pass rate statistics. Even if the final pass rate is 100%, this doesn’t mean there were no defects in the process.
Here is an example:
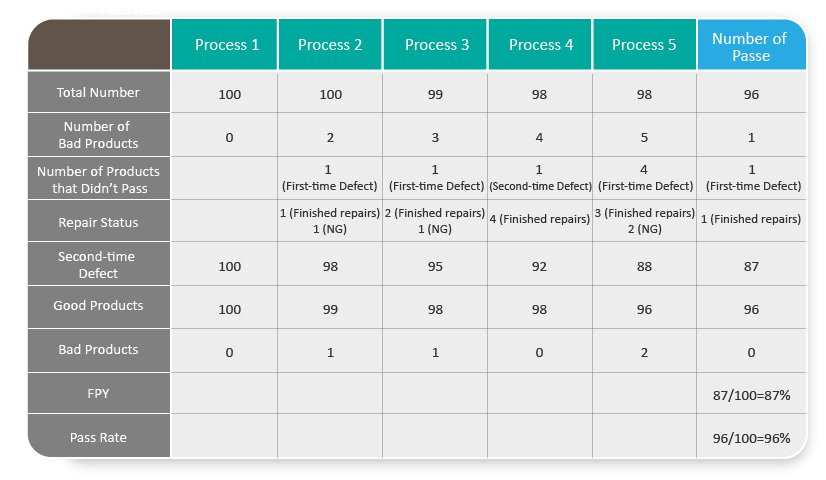
The first-time defect refers to a defect that is found the first time of inspection in the process. The second-time defect refers to a defect that is found again the same as the previous procedure.
It can be seen from the data in the table that the FPY of the product is 87%, and the pass rate is 96%. When using FPY and pass rate, the following points should be paid attention to.
The Difference Between FPY and Pass Rate
The pass rate only looks at results, regardless of what happened in the process. If there’s a defect in the process during manufacturing yet it has been fixed before the final inspection, it’s still counted as a good product. Even though the pass rate is sometimes high, the repair personnel in the factories can be very busy, resulting in a lot of wasted materials and repair hours. Even between different shifts or defective products on different days are repaired before the final inspection, they will still be counted as good products, resulting in differences in data.
FPY Looks at the Whole Process
If the product was picked out due to defectiveness in the previous process and becomes a good product after repairs, it still needs to be counted when calculating FPY.
For second-time defects, only one calculation is made. The FPY regards the whole process as a whole, so the relevant numbers are also a whole.
After calculating the FPY, you can see the issues in the result, providing pressure on the manufacturers because it seems like there’s always customer supervision. Repairing frequently not only drops the FPY, but the FPY of others will not increase either. This will result in the personnel that oversees the operation striving for the highest FPY.
The Pass Rate Regards the Entire Process as Separate Events
Even if the front-end engineers are repairing products daily, as long as they are repaired on time and accepted in the next stage, the final pass rate can still be high. However, this causes gaps in personnel at each process, lowering the efficiency of the production line.
Allion’s SMT quality management has a very complete system. Whether it is the quality inspection stage or the quality control stage, our professionals will strictly check the products. From product manufacturing to product shipment, we carefully count and analyze, implementing quality improvement and setting a standard that improves product quality. We meet our client’s needs and create benefits for our customers to improve the FPY. If you have related needs or inquiries, please feel free to contact us.
Allion’s SMT quality management features:
1. Good at finding issues, performing daily quality inspections and quality monitoring, and assisting clients in passing verification tests.
2. We stand from the perspective of our client’s profitability and assist them to improve their product quality and reduce costs, not just inspections.
3. We assist the factory in operating more smoothly and help with monitoring production, not just sampling products.
4. We carry out targeted and focused quality control starting from product design, rather than blindly expanding inspection efforts.
5. We Control, measure, monitor, and analyze the overall quality of the products and carry out planning and operations, input concepts, methods, and processes such as quality assurance, quality control, and quality improvement. We transform the abstract conceptual “quality” into real product quality.